Smart Watch Web
Energy efficiency for refineries and power stations.
In industrial facilities the use of steam is very common in very different processes such as, for example, heating raw materials in oil refineries or the rotation in thermal power plants to generate electricity.
This steam moves from the boilers where it is generated through the pipes through which it is channelled to its destination. There are numerous devices along these pipes that we call steam traps.
he steam traps are automatic valves that eliminate the condensate from the steam flow to make sure that the heat exchange process continues to be efficient. That is to say, the task of the steam traps is to eliminate the water from the steam pipeline that gets condensed in these in order to reduce the loss of heat energy throughout the piping.
The steam traps wear away over time, which might result in them leaking steam. Intelligent steam traps have sensors (temperature, ultrasound, pressure) thanks to which any steam leak in them can be detected.
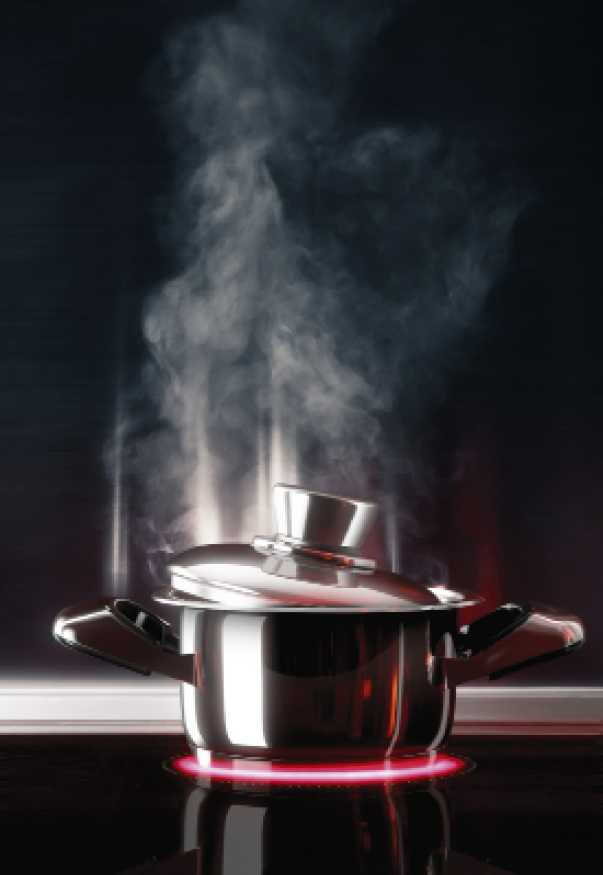
The SmartWatchWeb system is made up of a network of intelligent steam traps throughout the monitored industrial facility together with a computer system used to collect and process data from the sensors of the steam trap network and set off the corresponding leakage alarms, as well as issue the reports on the estimated energy losses, etc. A petrochemical plant might have hundreds or thousands of steam traps, each one of them might have steam leaks over time; on average between 15 - 25 % of them leak and these leaks can be reduced to up to 5 - 10 % with suitable inspection and maintenance programs.
The manual inspections of the steam traps in oil refineries requires weeks or months of work and experience of the inspection staff; that is why, they are only carried out every six months or annually. So, the time between the leaks and when they are detected and repaired is between 3 to 4 months; which results in huge energy losses. With the high price of energy the cost of steam in Europe is €25 - €30/Tm; each steam trap loses between €6000 and €9000/year. So the steam traps in a processing plant have energy losses valued at hundreds of thousands of €/year. In refineries, with thousands or tens of thousands of steam traps installed, these leaks raise the energy losses to several million €/year and they generate Tm/year of C02 emissions.
Solutions
The European Union (UE) in 2006 took legislative measures (Directive 2006/32/EC, among others) on the efficiency of the end-use of energy and the energy services, by establishing the need to use the best technology available to save energy, increase energy efficiency and reduce the effect of greenhouse gases.
As aforementioned, the SmartWatchWeb system helps detect leaks in real time, thanks to which these leaks can be solved in the shortest amount of time possible and therefore the enormous energy losses caused by these can be avoided. SmartWatchWeb can be considered to be a BAT (Best Available Technology) solution to comply with the European Directives as it helps attain the following objectives:
Immediately detect an internal or external steam leak.
Monitor the energy efficiency of the steam traps.
Reduce the CO2 emissions considerably.
Monitor the pressure of the steam mains
Monitor the backpressure of the condensate return network.
Case study
A Spanish refinery with more than 23,000 steam traps often had operational issues in its Sulphur Units due to problems in its condensate return network together with the internal and external leaks in its steam traps. The causes of the problem were identified and the possible solutions were analysed, opting to install intelligent bi-thermostatic steam traps BiTherm SmartWatchWeb[1], given that in the tracking apps, according to the thermodynamics, the bi-thermostatic steam traps provide 8% more energy efficiency than other steam traps (thermodynamic, inverted bucket steam traps, ball float steam traps, etc.).
With the solution adopted, each steam trap has external ultrasound and temperature sensors; 10% of them also have pressure and backpressure sensors. The SmartWatchWeb monitoring system collects all the information in one Website server that the personnel of the plant can access; additionally the energy service companies used carry out all the necessary repair work, and solve any incident detected by the SmartWatchWeb system in less than 24 hours.
Optimising energy of the network of steam trap stations of these Units has been possible thanks to the structural and functional features of the Bi-therm steam traps installed, because they have a pressure-balanced valve and an external adjustment device running. Therefore, the adopted solution is not invasive on either the monitoring or the repair work, so a considerable amount of money is also saved on the maintenance.
The results obtained in both Sulphur Units have been as follows:
Monitored steam trap stations
962 units
Investment made
1.656.210 €
Reduction of steam leaks
7,73 Tm/h
Reduction of CO2 emissions into the atmosphere
19.637 Tm/year
Energy saving (calculated at €25/Tm)
1.692.870 €/year
Savings due to the reduction of CO2 emissions
490.925 €/year
Total savings
2.183.795 €/year
Amortization period
9,1 months
Conclusion
The solution adopted in this refinery to increase the energy efficiency of the steam mains in its Sulphur Units has met the following objectives:
- Total fulfilment of the European Directives on energy efficiency.
- Total savings (energy and CO2): €2.18 million/year.
- Fast returns on investment: 9.1 months.
- Improved safety conditions in the Sulphur Units.
- Improved operations of the Sulphur Units.
Contact
You can get in touch with us by phoning us, sending us an email or by filling in the following form:
Telephone number
Commercial Department: comercial@soltecsis.com Technical Department: soporte@soltecsis.com
Address
SOLTECSIS SOLUCIONES TECNOLÓGICAS, S.L. B54368451 C/Carrasca, 7 local 3 03590 Altea (Alicante) - España (+34) 966 446 046 / 966 919 929 info@soltecsis.com
"*" indicates required fields